Custom Plastic Injection Moulding: Revolutionizing Manufacturing
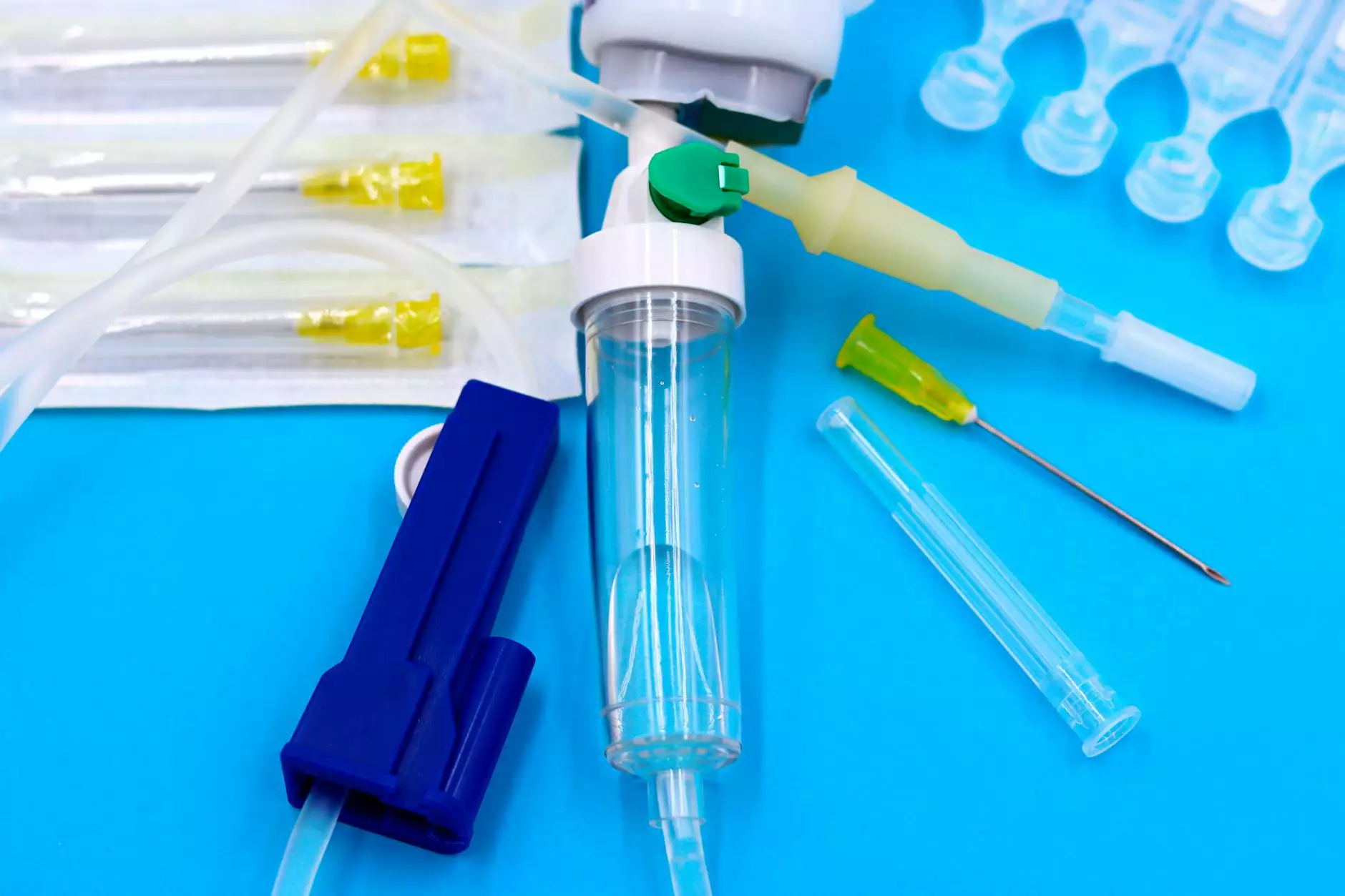
Custom plastic injection moulding is a crucial technique in the modern manufacturing landscape. It allows businesses to create high-quality, intricate components with precision and efficiency. In this article, we will delve deep into the many facets of custom plastic injection moulding, its advantages, applications, and how it can significantly benefit your business.
The Process of Custom Plastic Injection Moulding
Understanding the process behind custom plastic injection moulding is essential for anyone looking to leverage this technology. The process involves several steps:
- Material Selection: The first step is to choose the right type of plastic for your project, such as ABS, polypropylene, or polycarbonate. Each material has unique properties that may suit different applications.
- Mould Design: A precise design of the mould is crucial. It often requires CAD (Computer-Aided Design) software to create a design that will be both functional and efficient.
- Mould Creation: Once the design is final, the mould is manufactured using CNC machining or other high-precision processes.
- Injection: The plastic material is heated until it melts and is then injected into the mould under high pressure.
- Cooling: After injection, the material is allowed to cool and solidify, forming the desired shape.
- Demoulding: Finally, the mould is opened, and the finished part is removed.
- Finishing Touches: Parts may need secondary processes such as trimming, drilling, or painting.
Benefits of Custom Plastic Injection Moulding
Custom plastic injection moulding offers numerous benefits that make it a preferred choice for many industries:
1. High Efficiency and Speed
With the capability to produce thousands of parts quickly, custom plastic injection moulding is particularly beneficial for large-scale manufacturing. The cycle time is significantly reduced, allowing businesses to meet high demand with lower lead times.
2. Cost-Effective for Mass Production
Although the initial investment in mould design and creation can be substantial, the long-term cost savings are significant. Reducing the cost per unit as production scales makes it a wise financial choice.
3. Design Flexibility
Injection moulding allows for highly intricate and complex designs that may not be possible with other manufacturing methods. This flexibility caters to the unique needs of various industries.
4. Consistent Quality
Once the mould is made, the quality of the parts produced remains consistent. This reliability is vital for industries that require strict quality control, such as automotive and medical sectors.
5. Reduced Waste
Injection moulding produces minimal waste compared to other methods. The process allows for recycling of excess material, contributing to more environmentally friendly practices.
Applications of Custom Plastic Injection Moulding
Custom plastic injection moulding has a wide range of applications across various industries:
1. Automotive Industry
From dashboard components to exterior body parts, injection moulding plays a critical role in the automotive sector, offering durable and lightweight solutions.
2. Consumer Goods
Everyday items such as toys, kitchenware, and electronic housings are commonly produced using injection moulding, showcasing the versatility of the process.
3. Medical Devices
In the medical field, precision and reliability are paramount. Custom plastic injection moulding allows for the production of components that meet stringent regulatory standards.
4. Industrial Equipment
Many industrial tools and components, such as housings and brackets, are efficiently produced through injection moulding, ensuring both strength and functionality.
5. Packaging Solutions
The packaging industry benefits greatly from injection moulding, allowing for the production of customizable and lightweight packaging solutions that protect products.
Choosing the Right Partner in Custom Plastic Injection Moulding
Choosing a reliable partner for your custom plastic injection moulding needs is critical for the success of your project. Here are some important factors to consider:
- Experience and Expertise: Look for a company with a proven track record in your industry.
- Technology and Equipment: Ensure they use advanced technology and high-quality equipment for superior workmanship.
- Quality Assurance: Partner with a company that complies with industry standards and certification for quality assurance.
- Customer Service: Good communication and responsive service are vital for a successful partnership.
Conclusion
In conclusion, custom plastic injection moulding is an essential technique that can provide numerous advantages to businesses across various industries. Its ability to produce high-quality, cost-effective parts rapidly makes it an attractive option for manufacturers looking to improve efficiency and output. By understanding the intricacies of this process and choosing the right manufacturing partner, businesses can leverage custom plastic injection moulding to meet their specific needs and drive growth. Explore your options today at sumiparts.us and see how we can help elevate your manufacturing capabilities!