Precision Die Casting in China: A Comprehensive Guide
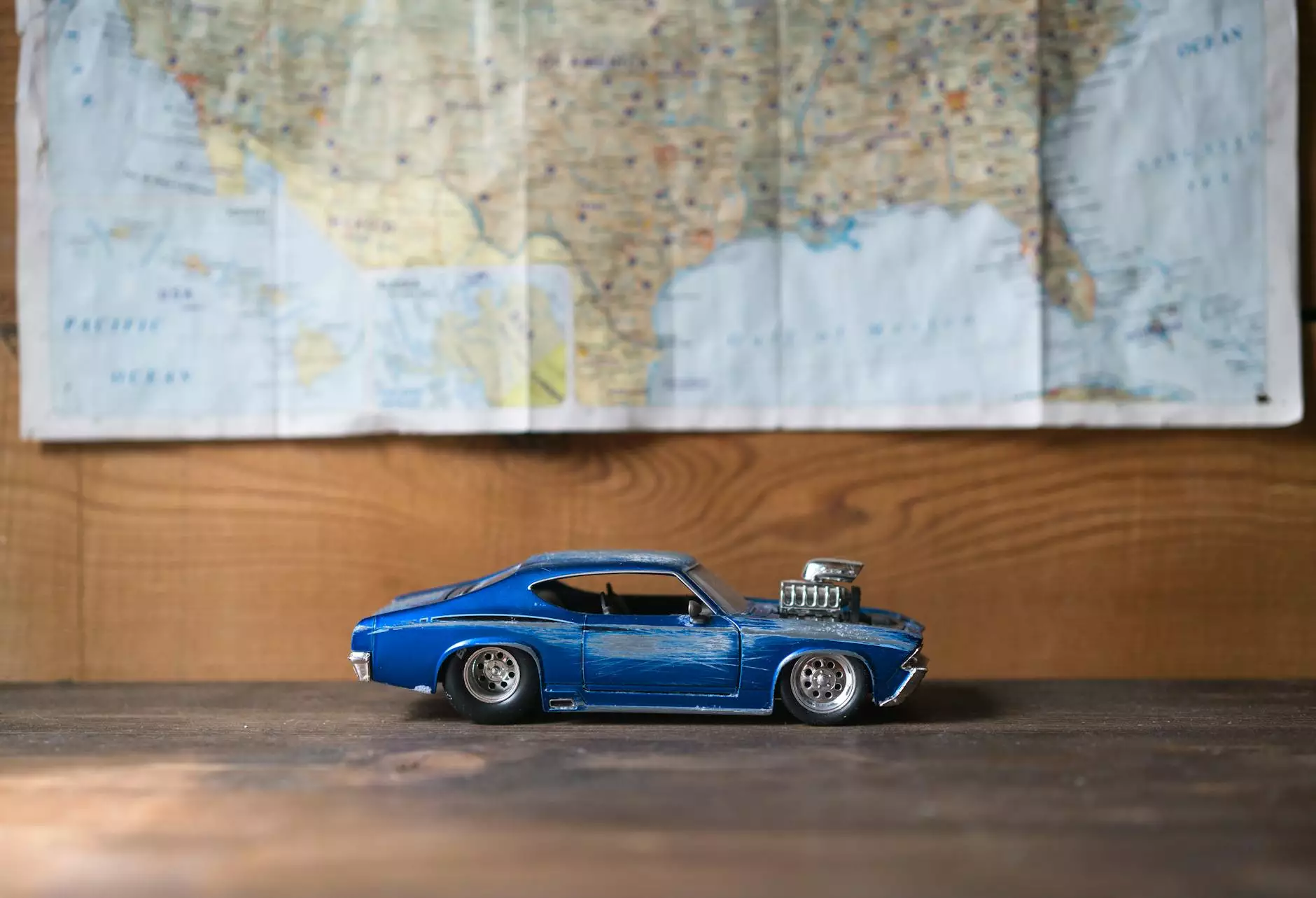
In the realm of manufacturing, precision die casting plays a pivotal role, especially in China, which has emerged as a global leader in this industry. This method of production is essential for creating high-quality metal parts with intricate designs and precise dimensions. In this article, we will delve into the various aspects of precision die casting in China, exploring its benefits, processes, and the factors making it a preferred choice for manufacturers worldwide.
What is Precision Die Casting?
Precision die casting is a specialized method of producing metal components by forcing molten metal into a mold under high pressure. This technique allows for detailed and complex shapes to be created with exceptional accuracy and minimal waste. The most commonly used metals in die casting include aluminum, zinc, and magnesium, each chosen for their unique properties.
Why China Leads in Precision Die Casting
China's dominance in the precision die casting industry can be attributed to several key factors:
- Cost-Effective Production: Labor costs in China are generally lower than in many Western countries, allowing for competitive pricing.
- Advanced Technology: Chinese manufacturers are increasingly adopting cutting-edge technology, including automation and high-precision machines, to enhance production quality.
- Skilled Workforce: China boasts a large pool of skilled laborers trained in advanced manufacturing techniques.
- Robust Supply Chain: The extensive infrastructure and supply chain in China enable efficient sourcing of raw materials and delivery of finished products.
- Government Support: The Chinese government has implemented policies to promote manufacturing, providing funding and incentives that benefit businesses in this sector.
Key Benefits of Precision Die Casting
When considering manufacturing options, it’s essential to understand the advantages of precision die casting, especially when sourced from China:
- High Dimensional Accuracy: The process produces parts that are extremely precise, often within tolerances of a few microns.
- Complex Geometries: Manufacturers can produce intricate designs that would be difficult or impossible with other manufacturing processes.
- Surface Finish: Die cast parts typically have a superior surface finish, reducing the need for extensive machining or finishing.
- Material Efficiency: High-speed production reduces waste, making it an environmentally friendly option.
- Enhanced Strength: Die cast components often exhibit enhanced mechanical properties, due to the rapid cooling process, which results in a denser material.
The Precision Die Casting Process
Understanding the precision die casting process is crucial for anyone looking to leverage this manufacturing technique:
1. Die Preparation
The first step involves preparing the die, which is usually made from hardened steel to withstand repeated use. The die should be precisely machined to achieve the desired specifications of the finished product, including details and features.
2. Melting and Pouring
Next, the chosen metal is melted in a furnace. Once at the correct temperature, the molten metal is poured into the die cavity. The pouring can be done using various methods, including gravity feeding, low-pressure, and high-pressure techniques.
3. Injection into the Die
For high-pressure die casting, the molten metal is injected into the die at high pressure. This quick injection helps fill intricate areas of the die, reducing defects and ensuring a perfect shape.
4. Cooling and Solidification
After the die is filled, the metal needs time to cool and solidify. The cooling process is critical, as it affects the final properties of the casting. Cooling times can vary based on the size and complexity of the part.
5. Ejection and Finishing
Once solidified, the die is opened, and the finished part is ejected. Additional finishing processes may be required, such as trimming excess material, polishing, or applying protective coatings.
Applications of Precision Die Casting
Precision die casting is utilized across a variety of industries, reflecting its versatility and capability for high-quality production. Here are some primary sectors that rely on this manufacturing technique:
- Automotive Industry: Components such as engine blocks, transmission housings, and other structural parts are often die cast.
- Aerospace Sector: High-performance components requiring strict tolerances, like brackets and housings, are produced using die casting.
- Consumer Electronics: Products such as housings for smartphones, laptops, and other electronic devices benefit from precision die casting.
- Medical Equipment: Precision components used in medical devices that require stringent quality standards are often die cast.
- Industrial Machinery: Many machines utilize die cast parts for durability and reliability in operation.
Choosing the Right Manufacturer in China
When looking for a supplier for precision die casting in China, consider the following factors to ensure quality and reliability:
- Experience: Look for manufacturers with a solid track record and experience in your specific industry.
- Certifications: Ensure the manufacturer has the necessary quality certifications, such as ISO 9001, that demonstrate adherence to international standards.
- Technical Capability: Review their machinery, technology, and the qualifications of their workforce to assess their capability to meet your demands.
- Client Reviews: Reach out to previous clients for feedback on their experiences regarding product quality and customer service.
- Communication: Choose a supplier that is easy to communicate with and responsive to your needs and concerns.
Future Trends in Precision Die Casting
The precision die casting industry in China is set to evolve with emerging technologies and changing market demands. Key trends include:
- Increased Automation: The rise of Industry 4.0 technologies is facilitating greater automation in die casting processes, enhancing efficiency and precision.
- 3D Printing Integration: The integration of 3D printing with die casting processes is expected to allow for rapid prototyping and more complex designs.
- Sustainability Efforts: As environmental concerns grow, manufacturers will increasingly adopt sustainable practices, including recycling materials and reducing emissions.
- Advanced Alloys: The development of new metal alloys tailored for die casting will improve performance and reduce costs for specific applications.
- Global Demand Growth: As more sectors recognize the benefits of die casting, demand for high-quality components is expected to rise, particularly in automotive and aerospace industries.
Conclusion
In summary, precision die casting in China offers a compelling solution for manufacturers seeking high-quality, cost-effective metal parts. With its numerous advantages, comprehensive manufacturing processes, and a significant presence across various industries, it’s clear why this method has become a preferred choice globally. Whether you're a small business or a large enterprise, leveraging the capabilities of Chinese manufacturers in this space can yield substantial benefits. As the industry continues to evolve, staying abreast of trends and innovations will be essential for businesses seeking to maintain competitive advantage.
Contact us at DeepMould for more information on how we can assist you with your precision die casting needs in China.
precision die casting china