Unleashing Innovation and Precision: The Ultimate Guide to a Leading Die Casting Mould Factory in Metal Fabrication
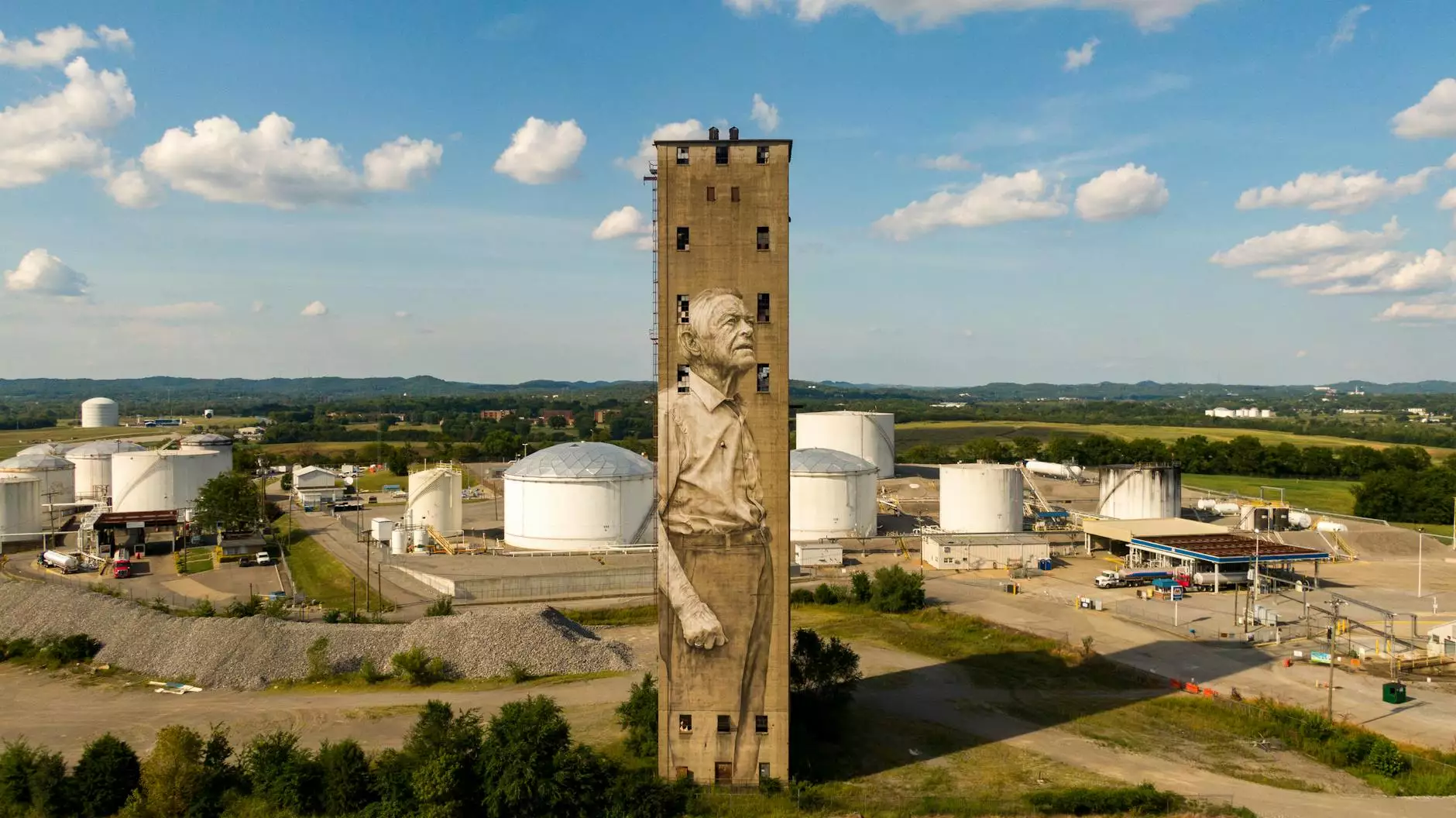
In the highly competitive landscape of metal manufacturing, the significance of high-quality die casting moulds cannot be overstated. As a cornerstone of precision metal fabrication, a die casting mould factory plays a pivotal role in elevating product quality, optimizing production efficiency, and fostering technological advancements. This comprehensive guide explores what distinguishes the top-tier metal fabricators in the realm of die casting, emphasizing the factors that make a die casting mould factory an industry leader.
Understanding the Role of a Die Casting Mould Factory in Metal Fabrication
Before delving into the attributes that define excellence, it's crucial to grasp the fundamental function of a die casting mould factory. These factories specialize in designing, manufacturing, and maintaining precision molds used in the die casting process—a manufacturing method where molten metal is injected into hardened steel molds under high pressure. The resulting components boast intricate designs, superior surface finishes, and high dimensional accuracy.
Their importance is underscored by the fact that the moulds themselves directly influence the final product's quality, durability, and performance. Therefore, a dedicated die casting mould factory must incorporate cutting-edge technology, skilled craftsmanship, and stringent quality control to meet the demanding standards of modern industrial applications.
Key Attributes of a Leading Die Casting Mould Factory
1. Advanced Technological Capabilities
Industry leaders in metal fabrication invest in state-of-the-art machinery, including computer numerical control (CNC) machining, 3D modeling, and simulation software. These tools enable precise mold design, allowing complex geometries and intricate details to be realized with minimal errors.
Utilizing CAD/CAM systems and virtual prototyping ensures that the molds are optimized for manufacturing efficiency and longevity, reducing cycle times and maintenance costs.
2. Skilled Workforce and Expertise
The craftsmanship behind high-quality die casting moulds requires a team of experienced engineers, mold designers, and precision machinists. Leading factories foster continuous training programs, promoting mastery in materials, heat treatment, and surface finishing techniques essential for durable molds.
3. Material Innovation and Quality Assurance
Top metal fabricators select premium-grade steel alloys—such as H13, SKD61, and SKD11—to manufacture molds with excellent thermal conductivity, wear resistance, and strength. Rigorous inspection routines, including coordinate measuring machines (CMM) and nondestructive testing, guarantee that each mold adheres to strict tolerances and safety standards.
4. Focus on Sustainability and Environmental Responsibility
Eco-conscious manufacturers utilize environmentally friendly lubricants, recyclable materials, and waste reduction strategies. Sustainable practices not only meet regulatory standards but also enhance corporate reputation and operational efficiency.
5. Customer-Centric Approach and Customization
Leading die casting mould factories work closely with clients to customize molds that meet specific project requirements. From prototype development to mass production, a flexible approach ensures rapid turnaround times and personalized solutions.
How a Die Casting Mould Factory Catalyzes Success for Metal Fabricators
Fostering Innovation through Precision
Innovation is the cornerstone of competitiveness. A top-tier die casting mould factory leverages research and development to introduce new mold designs, materials, and process techniques. This commitment to continuous innovation enables metal fabricators to create complex, lightweight, and highly functional parts for industries such as automotive, aerospace, electronics, and medical devices.
Enhancing Production Efficiency and Cost-Effectiveness
High-quality molds designed with advanced software and manufactured using precise machining reduce cycle times and defect rates. Consequently, manufacturers benefit from lower production costs, faster delivery times, and improved overall profitability.
Supporting Sustainability Goals
Efficient molds reduce material wastage and energy consumption, aligning with global sustainability initiatives. Companies partnering with environmentally responsible metal fabricators enhance their brand image and gain favor in markets with strict ecological standards.
Ensuring Product Consistency and Reliability
Consistent mold quality translates into uniform, defect-free products, which are critical in high-stakes industries like aerospace and medical devices. A seasoned die casting mould factory guarantees precision and repeatability across thousands of units.
Innovative Technologies Transforming Die Casting Mould Manufacturing
- 3D Printing and Additive Manufacturing: Facilitates rapid prototyping and complex mold geometries that traditional methods cannot achieve.
- Artificial Intelligence (AI) and Automation: Streamlines design optimization, predictive maintenance, and quality control processes.
- Laser Machining: Enables ultraprecise cuts and surface finishes, extending mold lifespan.
- Smart Materials: Development of mold materials with enhanced thermal and mechanical properties.
Choosing the Right Die Casting Mould Factory for Your Business Needs
Factors to Consider:
- Experience and Industry Reputation: Look for established factories with proven track records in your specific industry sector.
- Technological Infrastructure: Ensure they utilize up-to-date machinery, software, and testing facilities.
- Quality Certifications: ISO 9001, IATF 16949, and other relevant certifications indicate adherence to global standards.
- Customization and Flexibility: Ability to adapt molds to your unique specifications.
- Lead Times and Cost Efficiency: Efficient production cycles without compromising quality.
The Future of Die Casting Mould Factories in the Metal Fabrication Industry
As industries continue to evolve, especially with the rise of electric vehicles, smart electronics, and lightweight structural components, the demand for high-precision, durable, and innovative molds will intensify. Future die casting mould factories will increasingly adopt Industry 4.0 technologies, harnessing IoT, AI, and big data analytics to optimize manufacturing processes, predict maintenance needs, and further enhance mold performance.
Additionally, sustainability will play an even more significant role. Eco-efficient molds, recyclable materials, and greener manufacturing workflows will become standard expectations from clients worldwide.
Conclusion: Partnering for Excellence with a Die Casting Mould Factory
In conclusion, the success of your metal fabrication projects hinges heavily on the quality, precision, and reliability of your die casting moulds. A reputable die casting mould factory not only supplies essential components but also acts as a strategic partner, empowering your business with innovative solutions, cost efficiency, and sustainable practices.
At DeepMould, we pride ourselves on being a leading metal fabricators specializing in high-end die casting moulds. Our commitment to quality, technological excellence, and customer satisfaction makes us your ideal partner in achieving manufacturing brilliance. Whether you require custom molds for prototype development or large-scale production, we are dedicated to delivering exceptional results that help you stay ahead in the competitive market.
Get in Touch Today
Partner with DeepMould — your premier die casting mould factory. Experience the difference that cutting-edge technology, skilled craftsmanship, and unwavering quality can make in your manufacturing success.